Digital twins connect facilities and their spaces with individuals and the goals for which they are created. You may consider a digital twin as a replica of the construction project represented digitally that helps manage the project with a data-driven approach. Modern buildings generate data that can integrate into the digital twin, and decision-makers can utilize it for more efficient operations.
The tech has three essential functions: modeling, simulation, and management. Data modeling brings an understanding of how an object serves its residents and the quantifiable variables typical for it. Simulation enables facility managers to use data-driven insights for planning changes and adjustments and analyze how they will impact the space. Finally, management often deals with space, asset, or workforce management backed by collected data.
The best way to understand a digital twin is to consider it a database for the Internet of Things (IoT) and smart building systems. All data points from sensors or connected devices are collected in a digital twin, then the specific software pulls information to offer valuable insights regarding the building, which promotes informed decision-making and improves facility performance.
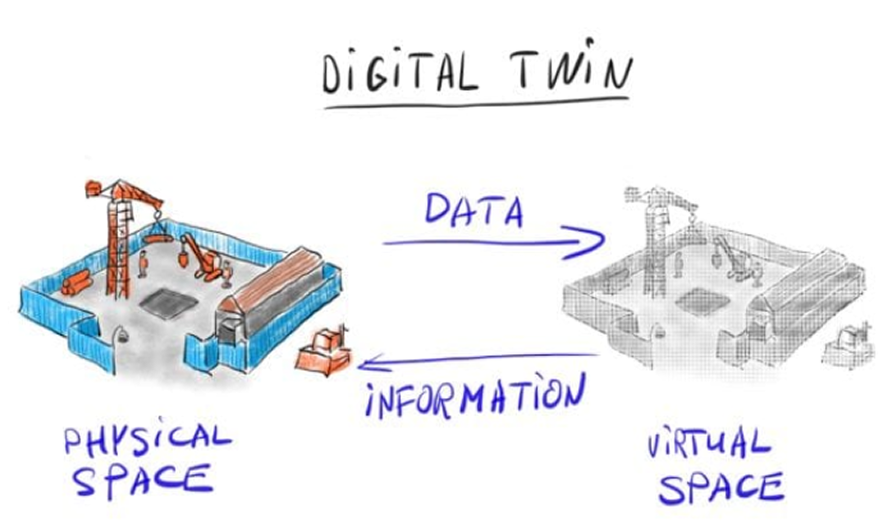
First, experts working with applied mathematics or data science research the relevant object's physical characteristics and operational information. This is crucial for developing a math model simulating the original.
After that, the developers building a digital twin guarantee that the virtual computer model will get feedback from sensors and other devices collecting data from a real-world facility. Thus, the digital replica can simulate everything happening with an original object in real-time. This creates opportunities to collect insights on building performance and various potential issues.
Ultimately, the complexity of digital twins depends on your requirements. The amount of information that determines your simulation's accuracy and precision may differ. You can utilize the twin with a prototype to provide feedback on the object during its development or as a prototype to provide modeling of what may occur with a building after construction is complete.
Implementing digital twin technology in construction helps address some critical challenges:

High Costs And Complicated Processes
Digital twins offer endless possibilities for reducing costs and optimizing processes. They enable construction firms to determine the likelihood of unpredictable outcomes, which opens opportunities for lowering maintenance costs and adopting more efficient practices during the project lifecycle.

Cooperation Issues
With a digital twin, project teams can track progress round-the-clock in real time. This improves cooperation efforts as all parties correctly understand project changes, updates, and statuses.

Performance Monitoring
As mentioned above, project teams obtain real-time remote progress monitoring, which helps increase their productivity and results in better project outcomes. This was impossible not long ago when employees relied on a strict location to work on large systems.

Improvements To Customer Experience
The tech allows for analyzing large data volumes to provide clients with the best results and receive feedback. Companies can propose relevant adjustments to ensure the desired outcomes by evaluating building performance quickly.
Although digital twin applications are common for various industries such as aerospace or manufacturing, construction is among those showing the most activity in the tech’s deployment. Now that we have learned about what a digital twin model is, let’s explore some of its use cases in the AEC industry.
• Utilities And Energy Consumption
Builders often adopt digital twins when designing, constructing, and maintaining utilities, power plants, etc. But the use of this technology has also increased for other types of facilities, like commercial and residential buildings. This is because a digital twin can significantly improve energy efficiency by providing managers with real-time information about energy consumption, so they can handle shortages or excesses accordingly.
• Urban Planning
Digital twins are helpful for the design of large construction projects. Moreover, the tech is vastly expanded to cover whole neighborhoods and cities, focusing on infrastructure. For example, the United Kingdom launched its National Digital Twin programme (NDTp) to leverage better outcomes from the country’s built environment. Meanwhile, thought leaders in the US also communicate the need to adopt digital twins as a means to “change the way governments plan their response to similar emergency and disaster scenarios.”
• Smart Cities
With a digital twin system, modern cities may facilitate more sustainable economic, environmental, and social responsibility practices. Virtual models of real objects can guide informed decisions and recommendations for the multiple complicated challenges cities must overcome. They involve transportation, energy consumption, etc. Thanks to real-time responses to emerging issues, the tech can enable mission-critical infrastructures like hospitals to operate more effectively.
• Disaster Management
The climate crisis has remained one of the most critical global issues in recent years. Fortunately, a digital twin system helps overcome this challenge by creating emergency response plans, constructing more intelligent buildings, and monitoring climate change.
Despite sounding similar in several ways, BIM and digital twins are quite different technologies. The confusion between the two relates to the fact that both provide digital visualization of buildings or structures. So, what is a digital twin vs. BIM in the AEC industry?

While BIM is responsible for constructing buildings, a digital twin is essential for managing them adequately. Thus, BIM helps with on-time, within-budget, and true-to-form design and construction processes. On the other hand, a digital twin enables a well-designed facility to achieve its purposes. Below, we will analyze both concepts on a deeper level through their benefits and drawbacks.
Benefits Of BIM
To understand how BIM can strengthen each project, it is crucial to learn about its most crucial advantages:
Money and material savings since BIM ensures accurate cost estimates before the beginning of construction.
Higher productivity and a shorter project lifecycle because of streamlined workflows and better coordination among trades.
Improved communication as all stakeholders can view BIM information and make suggestions which helps avoid data silos.
Prefabrication and modular construction which allows the manufacturing of necessary building components offsite, saving time and costs.
Challenges Of BIM
However, BIM implementation may also come up with its critical drawbacks, including:
Since BIM is a digital process, it needs investment in specific software solutions, which makes it a long-term investment for construction companies.
Being relatively new tech, BIM is still developing, so there is a lack of trained staff and experts in the industry.
Companies may find themselves in a situation where their partners or other contractors do not use BIM, which prevents them from utilizing relevant models.
Facility managers often ignore data collected in finished “as-built” models, including project specifications, which means wasted time and resources on the contractors’ side.
Benefits Of Digital Twins
Being virtual, digital twins promote the reduction of costs and risks regarding work on physical objects. Other crucial advantages are the following:
Increased operational efficiency with up-to-date information and quicker production.
Less costly research and development (R&D) activities because of the work with flexible and informative virtual prototypes.
More extended utilization of the facility’s systems and equipment since different maintenance issues can be analyzed through the digital twin model.
Improved building performance thanks to accurate real-time data.
Challenges Of Digital Twins
Companies aiming to create digital twins should consider the following challenges:
Data cleansing is frequently needed to make information from relevant CAD models or IoT-enabled devices usable within digital twin tech.
As digital twin data is transmitted through networks and software apps, securing it during all stages may be problematic.
Adopting IoT can significantly affect network infrastructure, information security, and management of connected devices.
The information stored in a digital twin is often voluminous and changeable.
The growing implementation of digital twins and BIM during the construction project lifecycle is not accidental. It is a must-have today since modern facilities are more complex than ever, with multiple complicated systems working cohesively. People also expect more from their building spaces, and companies intend to find new practical approaches to maximizing available space and getting a higher return on investment (ROI).
Ultimately, BIM and digital twins are crucial for proper lifecycle management. But which one should you choose for your project? The answer depends on your requirements. While BIM simplifies design and construction processes, a digital twin helps manage complex spaces efficiently and meet all owner’s expectations. The best option is combining both technologies as they will make buildings more dynamic, from the conception stage to being fully operational.
Are you thinking about improving your construction project with BIM and digital twins? Contact us today to discuss how we can assist you in achieving your goals.